
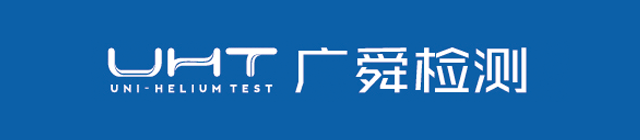
摘要
越来越多锂电池公司认识到在密封性检测方面,采用氦检替代传统气检,在检漏效率和检漏精度方面可以实现大幅提升。
安全是动力电池永恒的话题。
近年来,中国新能源汽车产销量持续增长,带动整个新能源产业链发展壮大。然而新能源汽车起火事故也在逐年攀升,行业乱象频出,动力电池安全屡次被推上舆论的风口浪尖。
当前,各大电池企业都在积极改进制造工艺和升级产线,从制造层提升产品品质。同时电池企业也在采用各种检测手段进一步提升电池的安全性,其中泄漏检测是把关电池安全必不可少的环节。
众所周知,泄漏会让锂电池出现电解液挥发、水分渗入、鼓胀等诸多问题,进而导致锂电池性能下降乃至起火爆炸。电池壳体的密封性直接决定了电池的安全性能,因此提高锂电池泄漏检测的精度和效率至关重要。
目前,越来越多锂电池公司认识到在密封性检测方面,采用氦检替代传统气检,在检漏效率和检漏精度方面可以实现大幅提升。
值得注意的是,当前行业普遍认为锂电池氦检就是一次氦检和二次氦检,而广舜检测技术(上海)有限公司(以下简称:广舜检测)却对此拥有不一样的理解并提出更优的解决方案。
广舜检测总经理应武认为,目前锂电行业方形铝壳电芯在氦检方面存在以下痛点:
痛点1:氦检设备买的起但检测成本高昂
氦检设备采用氦气作为示踪气体进行电芯的泄漏检测,这个过程必然会消耗氦气。但在实际应用中,锂电池行业的普遍现状是,氦气消耗量过大导致电池企业检测成本上升。
以盖板周边焊后,注液前的氦检工位(行业一般称为一次氦检,或者前氦检)为例,目前行业常见的12ppm节拍的一次氦检设备,1罐40L/13.5MPa的氦气,只能测试2-5万个电芯,年消耗氦气费用在20-40万元之间。
再加上二次氦检的氦气用量,一条12ppm的产线,年消耗氦气在30-50万人民币之间,按5年折旧测算,该条12ppm的产线在全生命周期内需花费氦气150-250万元。
氦是宇宙中第二丰富的元素但在地球上的含量极为稀少,用途广泛,是一种战略资源。中国的氦气主要依赖进口,成本高昂。在此情况之下,氦气消耗过大会导致电池企业检测成本增加,不利于企业提升竞争力。
痛点2:二次氦检难以解决封口焊后的密封性检测问题
封口焊接是方形铝壳电芯最后一个密封工艺。传统解决封口焊后密封性测试思路,是采用二次氦检机。
但在实际应用中,二次氦检后的电芯在封口处依然有偶发的漏液现象发生。
原因是电芯在二次氦检过程中,由于胶塞的阻断作用,原本作为示踪气体的氦气,无法到达铝片焊接处导致检测失效。
总体来看,目前锂电池二次氦检检出的不良品可分为:误判,盖板周边焊的不良,极少部分的封口焊接不良(胶塞不良)等。这意味着二次氦检还需进一步优化。
作为一家革新的国际高品质泄漏测试方案提供商,广舜检测致力于提供更可靠的检漏方法。针对上述痛点,广舜检测针对性的推出了高性能前氦检机和封口铝片氦检机,解决氦气消耗大和检测不完善的问题。
其中,广舜检测推出的高性能前氦检机可以大幅提升检测效率,在12ppm产线上1罐氦气可以检测百万个电芯,大幅提升电芯品质。配合公司研发的高效氦气回收机,可节约95%以上的氦气费用。
同时也可以减轻锂电池企业在氦气采购、存储、运输、更换等方面的压力,助力电池企业进一步降本。
相比前氦检,封口铝片焊接的密封性检测难度更大,进而对检测设备提出更高的要求。
对此,广舜检测历时2年研发推出封口铝片氦检机,该设备可守住胶钉老化失效后的密封防线,极大程度杜绝水汽、杂质进入电芯,从而防止电解液泄露。
业内人士认为,从产品质量提升角度来看,电池厂会越来越重视氦检,同时也对氦检设备企业提出更高的要求。而广舜检测致力于提供更可靠的检测方法,为锂电行业带来新的氦检思路和方案,进一步提升国产电池安全和性能。
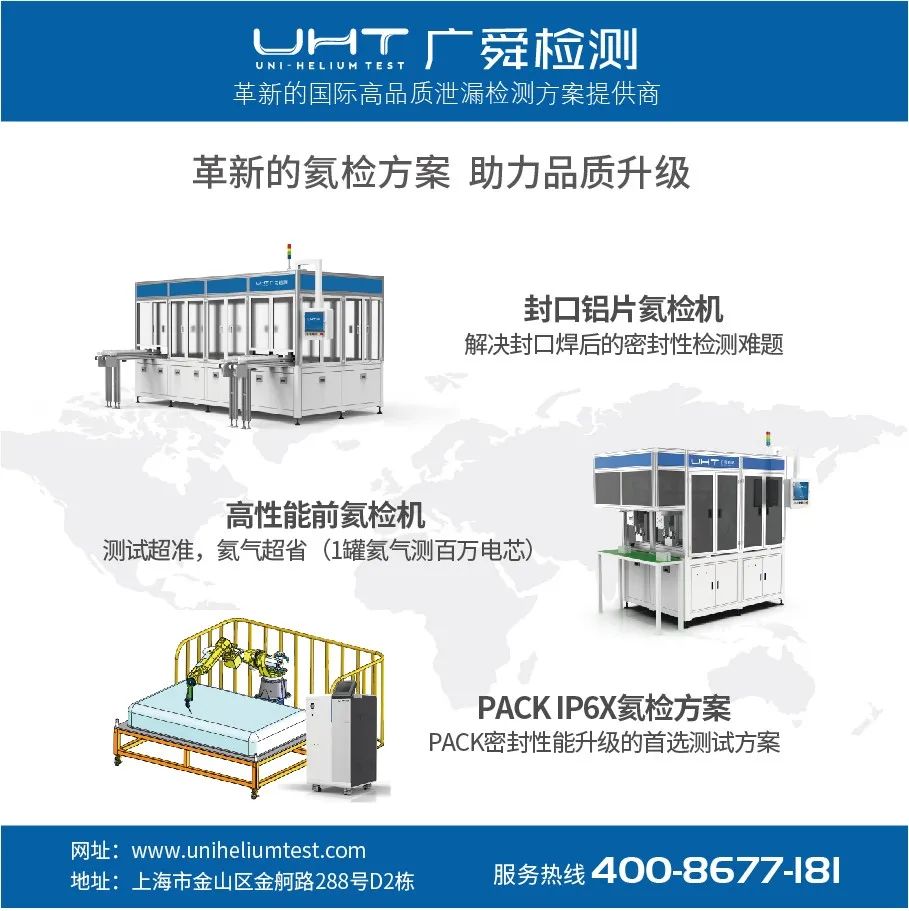
↙点击下方“阅读原文”查看更多内容。
|